TECHNOLOGY技術情報
表面処理製品DLC(ダイヤモンドライクカーボン)とは
DLC(ダイヤモンドライクカーボン)とは、ダイヤモンドに近い特性を持つ非結晶(アモルファス)の硬質膜のことです。このDLCはプラズマを利用して物質にコーティングすることが可能です。コーティングされた物質の表面は、硬さや滑り性が向上し、薬品に対しても強くなるなど、製品の耐久性がアップします。
ダイヤモンドはsp3(ダイヤモンド成分)(※1)という結合からなる結晶構造を持ち、グラファイトはsp2(炭素成分)(※2)という結晶構造で出来ています。DLCはそのsp2とsp3が混在する形で形成されている皮膜です。
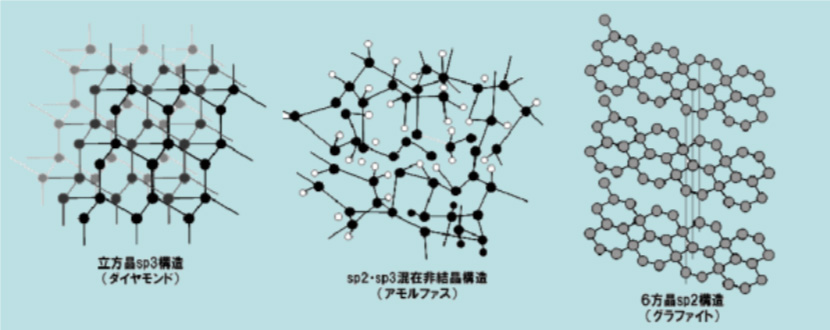
※1【sp3とは】
ダイヤモンドのそれぞれ炭素原子は、他の4つの炭素原子と3次元的に結合したダイヤモンド構造と呼ばれる状態をとっています。炭素原子が緻密に充填しているので、結びつきがとても強く、それがダイヤモンドの硬さと独特な輝きを与えているのです。
※2【sp2とは】
グラファイトは、蜂の巣状に結合した炭素原子の平面が重なった状態をとっています。それぞれの炭素平面は、弱い力で結ばれているので、容易に剥がれます。そのため、鉛筆で紙をこすると剥がれた炭素の層が紙に付着して字を描くことができます。
当社では、産業技術総合研究所と共同開発したPBII&D(プラズマイオン注入・成膜技術)という独自の技法を用い、従来では難しかった大型基材への均一なコーティングや、立体形状物への成膜、熱に弱い素材への成膜も可能としました。
DLCに関しましては当社で受託加工も承りますが、成膜装置の販売も行っております。
DLCの特徴
1
高硬度
ビッカーズ硬度(※3)で1000〜7000Hvの硬度があり、ダイヤモンドに次ぐ硬さです。
2
低摩擦
摩擦係数が非常に低く、耐摩耗性が大幅に向上します。
3
耐薬品性
バリア性が高い皮膜で、様々な薬品の影響を防ぐ事ができます。
4
耐環境性
製造工程において廃液などが発生せず、かつ炭素が主体の皮膜なので人体にも影響がありません。
ビッカーズ硬度とは、ダイヤモンド圧子で押し込み、その凹みの大きさから硬度を算出する方法です。単位は[Hv]で、Hardness Vickersの略称です。
当社のDLC成膜法PBII&D(プラズマイオン注入・成膜技術)
一般的にDLC成膜に用いられている、PVD法やPCVD法とは異なる新しいDLCコーティング技術です。
従来の成膜技術の欠点であった点を解決すべく、開発したプラズマイオン注入はアメリカのGEとロスアラモス研究所が開発したが成功する事が出来なかった技術を更に進化させ、基材自身でプラズマを発生させ成膜することにより、自公転不要で立体形状物に成膜することが可能になりました。
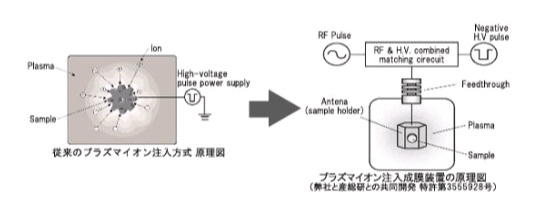
従来はRFアンテナでプラズマを生成し、高電圧を基材に印加することで、プラズマを引き付けていたため、プラズマの濃淡が発生し均一にコーティングすることが難しかったのですが、新技術では基材に直接RFと高電圧を印加する特殊技術の開発により、基材自身でプラズマを生成し、プラズマを引き付ける事が可能になったため、三次元形状に均一にコーティングすることを実現しました。
従来のDLC成膜法、PVD法とPCVD法について
PVD法は、ターゲットから固体材料を飛ばし、コーティング対象に付着させ、膜をコーティングするため、ターゲットの位置により膜の付き回りに差が出るため、自公転が必要です。
PCVD法は電極の陰極側にコーティング対象を置き、陽極側からガス化させたプラズマを照射する形で膜をコーティングするため、 電極設置部分は膜が付かなかったり、電極の構造により膜の付き回りが大きく差が出てしまいます。
PBII&D(プラズマイオン注入・成膜技術)の工程
プラズマイオン注入成膜装置では以下の工程でプラズマが生成されます。
- (a)真空装置内へガス導入
- (b)高周波電源(RF) ON
高周波電源ONすることで、処理物の周りにプラズマが生成されます。 - (c)高周波電源(RF) OFF
基材周囲のシース(※1)が無くなり、プラズマが漂っているような状態に。 - (d)高圧パルス電源 ON
基材周囲のイオンを高電圧パルスで基材へ引き込むことで、イオン注入やDLC成膜を行える。 - (e)高圧パルス電源 OFF
基材周囲のシースが無くなり、
アフターグロープラズマ(※2)によって更に成膜されている。
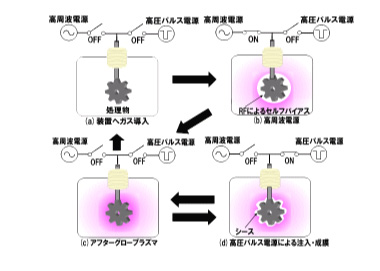
※1 シースとは(-)の電気の印加によって、質量が軽い電子が飛ばされ、重いイオンのみが存在している領域で、成膜には重要な領域
※2 アフターグローとは電離した電子とイオンが元の状態に戻ろうとする領域です。電子温度も下がり、プラズマ密度も低い状態で、ラジカルと呼ばれる成膜には重要な物が生成され、DLCを更に形成していきます。
プラズマイオン注入装置では工程によって、
プラズマを使い分けDLC成膜などを行っています。
【クリーニング工程】
クリーニング工程では、Arプラズマと水素プラズマを利用して基材のクリーニングを行います。Arプラズマによって、 基材表面に付着している汚れ成分や酸化皮膜などを除去し、水素プラズマによって、基材から離れた成分を化学結合させ、 排気して基材表面をクリーニングします。これがDLCの密着力に大きく影響します。
【DLC成膜】
クリーニング後に、DLC成膜工程へと移ります。炭素を原料とするガスをチャンバー(※3)内へ導入し、プラズマを立てる事で、 基材に炭素イオンが付着しています。この作業を繰り返す事で、基材表面にDLCが成膜されます。
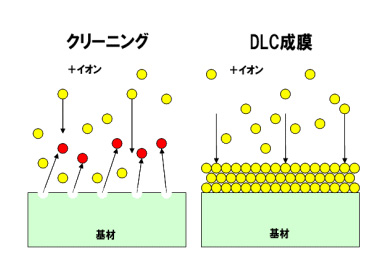
※3 チャンバーとは真空するための容器(小さな部屋)
PBII&D技法で進化したDLC成膜
立体複雑形状への成膜
基材自身を電極として周囲にプラズマを発生させることで、立体複雑形状の基材に対して均一にコーティングすることが可能となりました。
扱える皮膜の幅が拡大
基材に電界を直接発生させることでプラズマ状態をコントロールすることができ、イオンのコントロールまで可能になったため、従来より扱える皮膜の幅が広がりました。
大型基材へのコーティング
自己放電プラズマの技術により、 ワーク表面積が大型化してもワーク自身をプラズマ発生源として用いるため、均一にDLCコーティングを施せます。
低応力・厚膜のコーティング
従来のDLC成膜技法と比較して高いバイアス電圧を印可することにより、低応力のDLCコーティングを実現しました。また膜の内部応力を低く抑えることで、厚膜コーティングも可能となりました。
室温からの低温成膜
バイアス電圧をパルスで印可することにより出力制御して、室温で低温成膜することができます。
DLCの用途
- 自動車業界
- 電磁クラッチ,バルブリフター,ピストンリング,ガスケット
- 半導体業界
- ウェハラッピングキャリア,各種搬送部品
- 電機業界
- シェーバー,スピーカー,磁気テープ,光学メディア
- 食品業界
- 生鮮品切断刃,パン切り刃,製麺用ロール,ペットボトル
- 医療業界
- チューブ,義肢部品,ステント,義歯部品
- その他
- 切削工具,ライター等の装飾,腕時計,ゴルフクラブ等
様々な分野で、様々な製品に利用されています。